DLAMP is a revolutionarily joining technology for metal and dissimilar materials by use of laser.
Secure joint with dissimilar material is achieved by creating anchor structure on the metal surface by laser treatment.
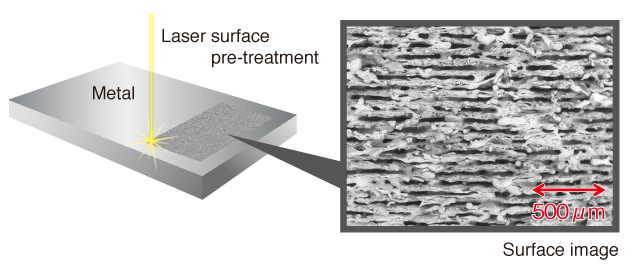
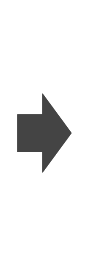
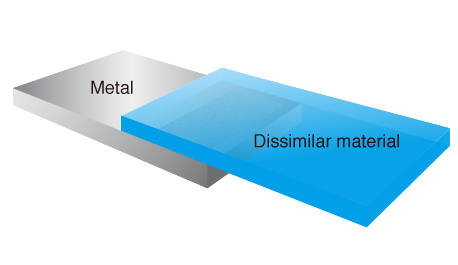
- Features
- 1. Applicable to various metal
- 2. No masking is required for partial treatment (Single-side treatment and patterning is possible)
- 3. Small environmental load (No chemical waste)
The Mechanism of DLAMP
Anchor Effect :
The high joining strength is achieved by molten materials permeating through the voids (undercuts and tunnel-like structures) formed on the metal surface by DLAMP treatment.
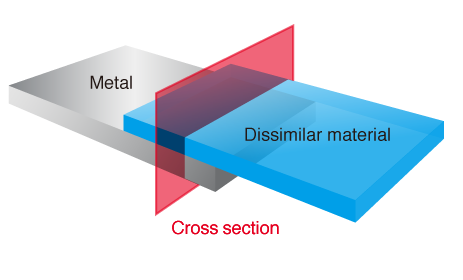
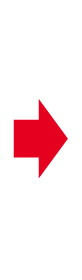
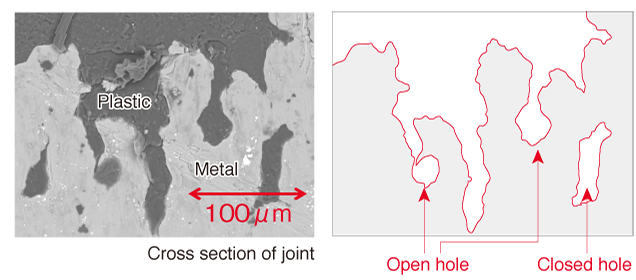
Powered by kanazawa Institute of Technology
Masashi YAMABE –Masahiro SETO Laboratory.
Composite molding
Injection molding
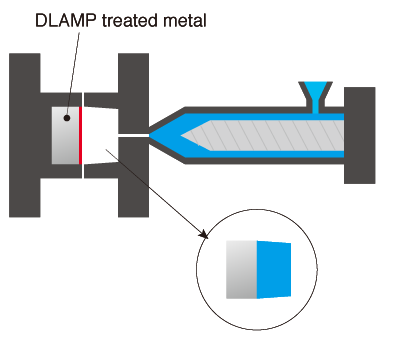
Compression molding
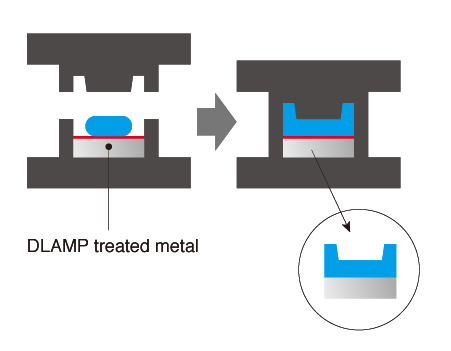
Dispencing
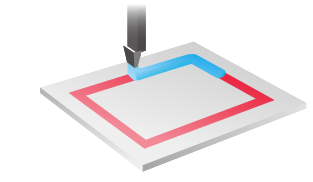
Spray coating / Thermal spraying
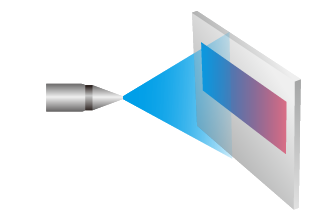
Examples of applications
Insulation / Sealing
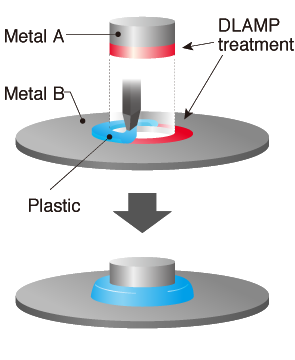
Gasket
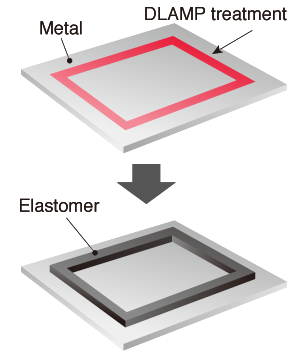
Metal Insert
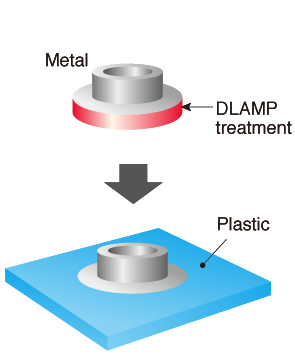
Shaft
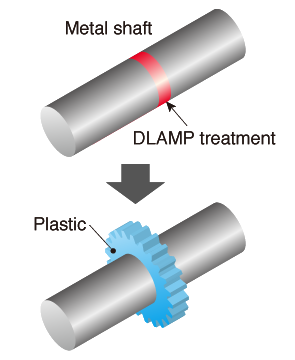
Applicable metal
Metal | Experience | |
---|---|---|
Aluminum alloy | A2017 | |
A5052 | ||
A6061 | ||
A7075 | ||
ADC12 | ||
Stainless alloy | SUS304 | |
Iron alloy | SPCC | |
SS400 |
Metal | Experience | |
---|---|---|
Magnesium alloy | AZ31 | |
AZ91D | ||
Titanium alloy | Titanium(TP340) | |
Titanium64(TAB6400) | ||
Copper alloy | Copper(C1100) | |
Brass(C2801) | ||
Nickel silver(C7501) | ||
Zinc alloy | ZDC2 |
: Well experienced : Experienced
Coated metal
Aluminum alloy | Alumite |
---|---|
Iron alloy | Chromate steel plate |
Zinc plating | |
Electrodeposition coating | |
Copper alloy | Tinned copper |
Joint Strength
Thermoplastic
Tensile strength (MPa) | Shear strength (MPa) | |
---|---|---|
PP/LGF40 | 25 | 20 |
PBT/GF30 | 35 | 35 |
PA66/GF30 | 50 | 50 |
PPS/GF40 | 50 | 50 |
PC/GF40 | 30 | 25 |
Metal : A5052
Test method : ISO 19095-3:2015
Elastomer
Tensile strength (MPa) | Elongation at break (%) | |
---|---|---|
Silicone elastomer hardness 80 | 2.2 | 40 |
Fluoroelastomer hardness 60 | 5.5 | 150 |
Fluoroelastomer hardness 80 | 6.0 | 100 |
Metal : A5052 Test method : JIS K 6253
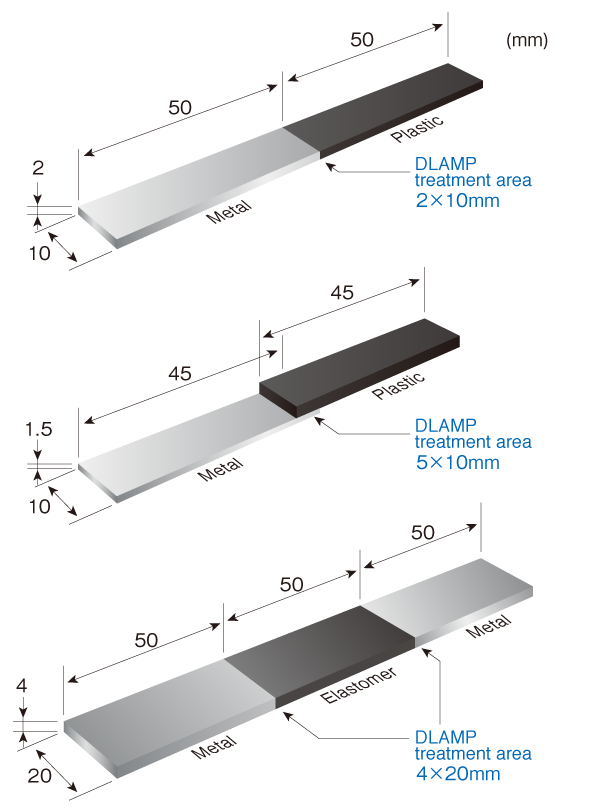
Technical Information
Airtightness data
(helium leak test)
Using DLAMP® treatment metal produce good airtightness.
- Plastics
- PPS/GF35%
- Test
- Helium leak
Surface pre-treatment | Non-treatment | DLAMP®-treatment(width:5mm) | |||
---|---|---|---|---|---|
Metal | Aluminum alloy A5052 | Aluminum alloy A5052 | Stainless steel SUS304 | Brass C2801 | Magnesium alloy AZ91 |
Helium leakage quantity |
|||||
Helium leakage quantity (After heat cycle test) |
: A leakage quantity ≦ 5×10-7 Pa・m3/s
: A leakage quantity ≧ 5×10-5 Pa・m3/s
*Heat cycle test : -40°C (30 min) ⇔ 125°C (30 min), 500 cycles
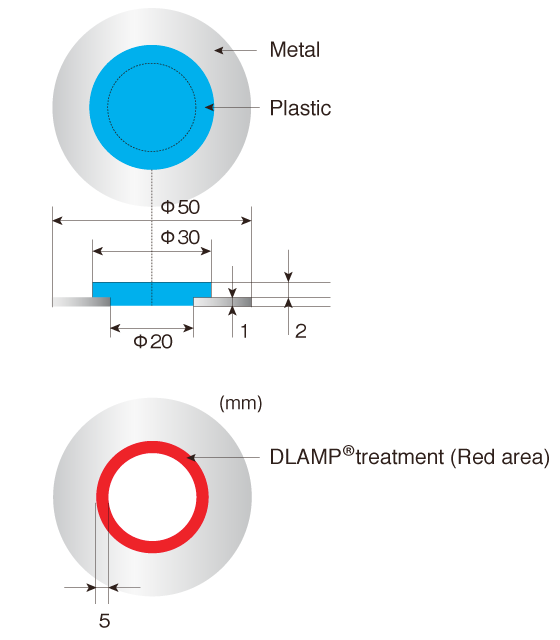
Joint durability
Heat Resistance test
- Test condition
- 120°C,500hr
- Test time
- 500hr
- Metal
- SUS304
- Plastics
- PP-LGF40
PA66-LGF30
PA66
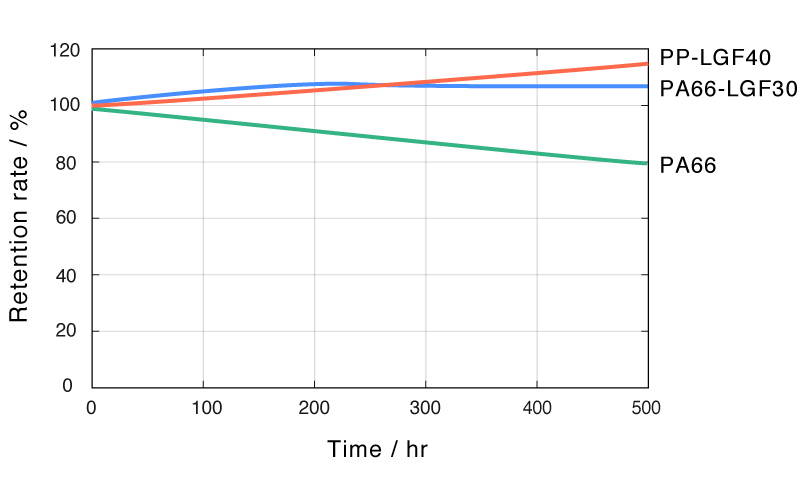
Heat cycle test
- Test condition
- -40°C,1hr ⇔ 90°C,1hr
- Test time
- 1000hr
- Metal
- SUS304
- Plastics
- PP-LGF40
PA66-LGF30
PA66
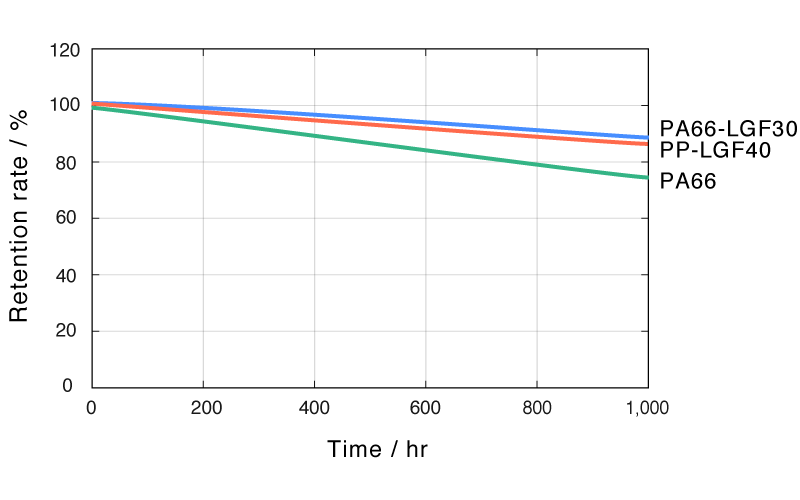
DLAMP® treated samples
Anodized aluminum
- Form
-
Metal | Anodized aluminum |
---|
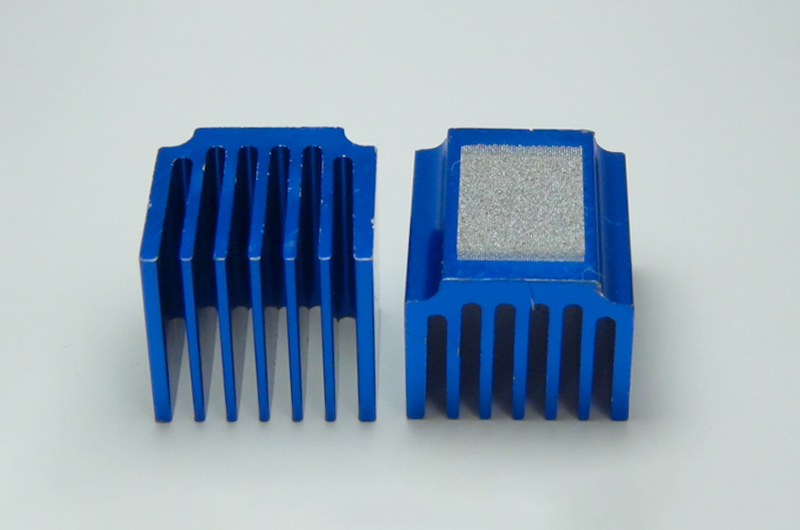
Heatsink
- Form
-
Metal | Copper plating Aluminum |
---|
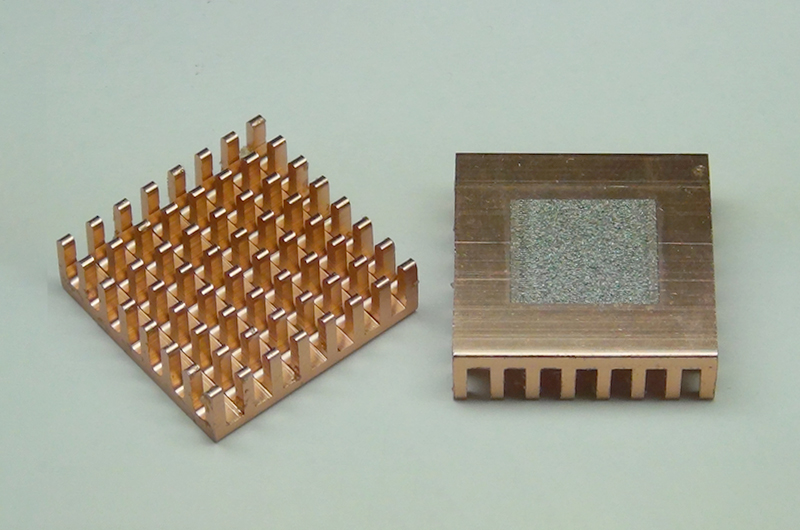
Coated iron plate
- Form
-
Metal | Electrodeposition coating iron |
---|
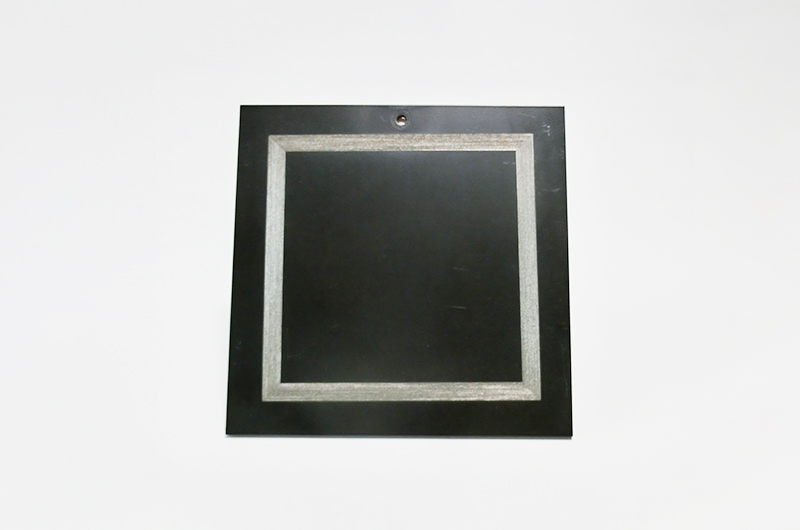
Brass pin
- Form
-
Metal | Brass |
---|
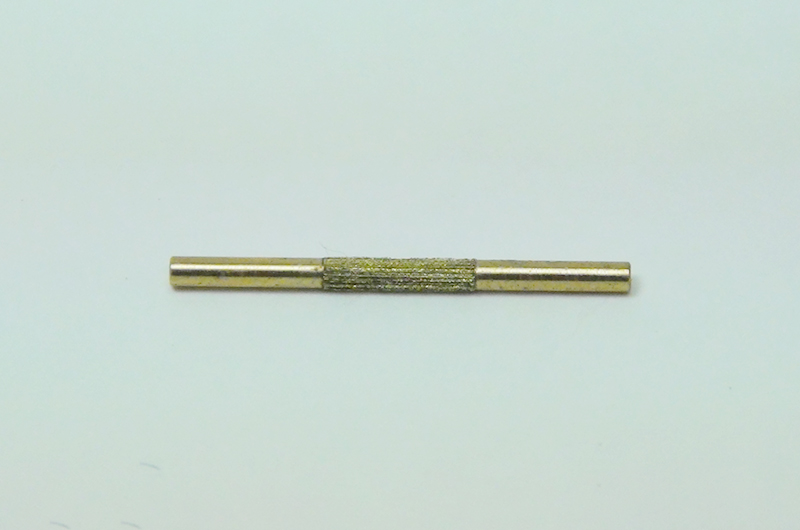
SUS Pipe
- Form
-
Metal | SUS304 |
---|
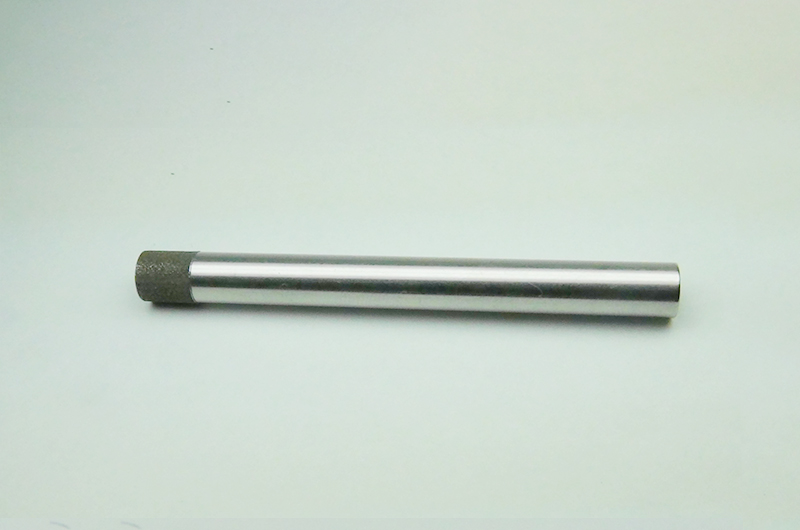
Tube
- Form
-
Metal | SUS304 |
---|
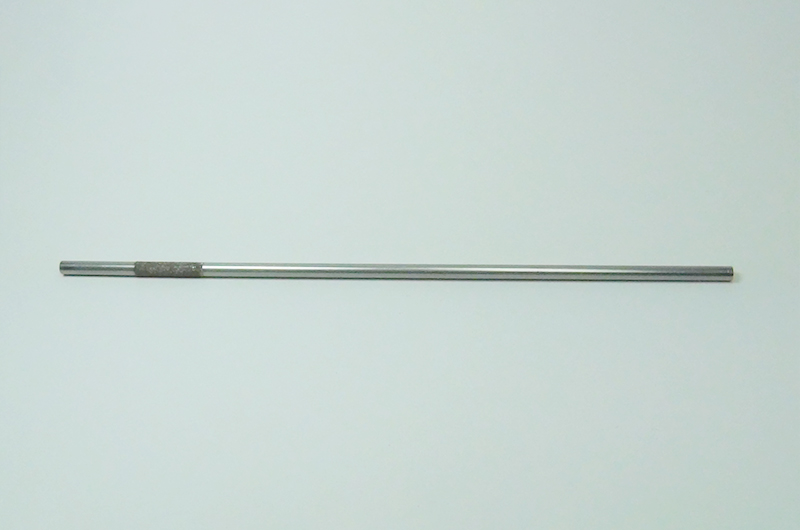
Washer
- Form
-
Metal | SUS304 |
---|
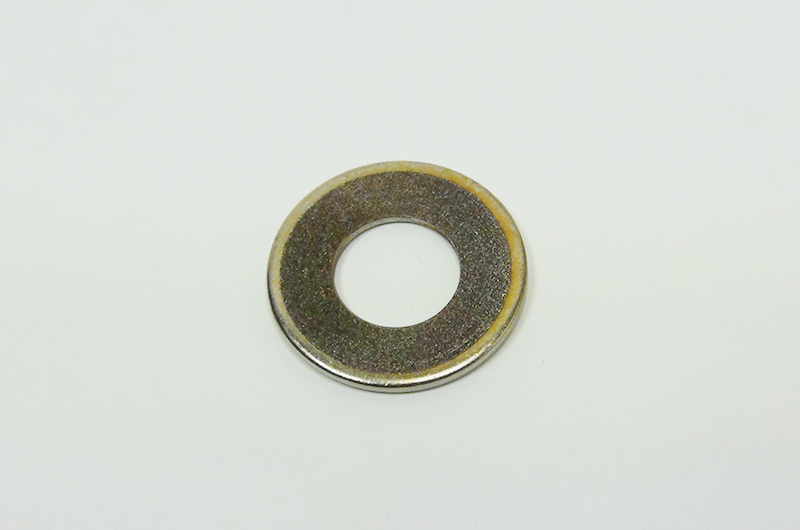
The information contained herein is all the data available at present.Unauthorized copying prohibited.
DLAMP® is a registered trademark of Daicel Miraizu Ltd.